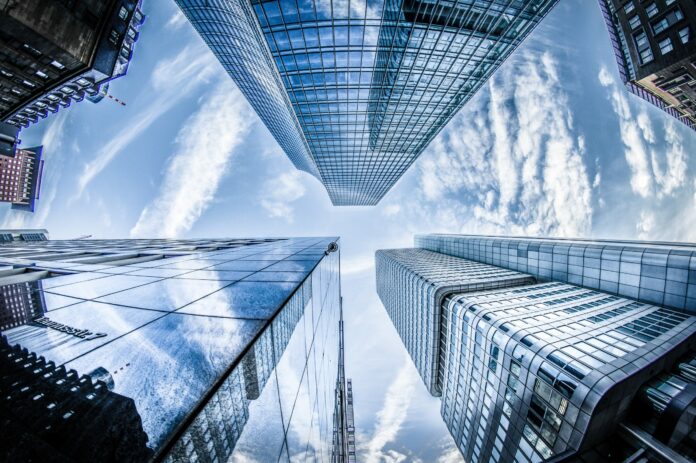
Spray operations involving building materials require specific tools. From small projects to major renovations, we have all of the right equipment available for every task at your fingertips.
Contrary to elliptical and circular nozzles, rectangular nozzles can achieve higher particle velocities; however, chemical reactions often take place in them that lead to clogging (Ref 38), creating an obstacle for long-term operation of cold spray equipment resulting in decreased coating quality. Spray equipment for sale should be of high quality to ensure prolonged and efficient use for precision jobs and well-organized construction.
High Volume Low Pressure (HVLP)
HVLP utilizes low air pressure and high volume of air for spray atomization and to decrease forward velocity, thus minimizing overspray pollution and waste material compared with a traditional spray gun.
Use this machine with nitrogen, helium or compressed air as working gas for maximum flexibility and powder feeding rates of 120 grams/minute. With circular or elliptical nozzle options and high velocity potential it can deposit materials that are difficult to cold spray such as stainless steels, titanium alloys and Inconel (Ref 56).
Distributor of spray guns, such as HVLP and low volume medium pressure (LVMP) sprayers. Provides complete systems or a selection of finishing, pumping, application dispensing & control products suitable for manual, automatic and robotic operation; additionally offers lubrication printing ink delivery and cleaning systems and parts to serve aerospace, wood refinishing, protective coating refinishing as well as automotive refinishing industries.
Airmix (AAA)
Airmix(r), developed by Sames in 1975, is a medium pressure spraying technology that combines conventional Airspray with high pressure Airless technologies for maximum finish quality and rapid payback, meeting environmental protection policies. The latest generation Xcite gun features an ultra light trigger to increase comfort while decreasing risks of Repetitive Strain Injury (RSI). An atomization aircap adapts to fan spray pattern width reducing fluid consumption and optimizing performance; all while offering three pressure range options ranging from 120, 200 & 400 bar (1740-2900-5400psi). Trolley & Hopper are optional extras!
The Kremlin Rexson 30C25 and 15C25 pumps are powerful pumps designed for medium to large productions (kitchen cabinets, industrial equipment etc). Their perfect balance between fluid flow rate and finishing quality allows HVLP spraying technology to produce optimal results.
Conventional
Conventional spray equipment for sale utilizes compressed air to atomize its product, producing considerable overspray and mist that travels long distances; this can be reduced with proper gun size and pressure settings as well as using various nozzle sizes and attachments designed for specific uses.
Conventional guns come in two primary varieties – single and double nozzle. Both types can be placed both horizontally and vertically to be sprayed over parts. This system, commonly known as rotary atomizer, is often found on automatic lines utilizing conveyors loaded with parts to be sprayed over.
Conventional spraying equipment is highly versatile when operated by an experienced applicator, capable of applying various coatings with low viscosity, low flow rate and high production output. Unfortunately, it often incurs costly organic solvent thinning and disposal fees as well as contributing to photochemical smog emissions.
Cold Spray
Cold spray uses a high velocity stream of metal powder particles accelerated at supersonic speeds in order to form bonds and embed themselves onto components’ surfaces. This technique is useful in producing corrosion-resistant coatings (zinc and aluminum), dimensional restoration and repair services, high strength dissimilar material coatings for manufacturing applications and field repairs of components and structures.
This process employs a highly compressed gas jet containing metallic and nonmetallic powders heated below their melting points and fed through an injecting gun equipped with a level type convergent-divergent nozzle enabling rapid injection at high velocity.
On impact with the component, powder particles experience extreme plastic deformation and bond to form a coating. This is one of few thermal spray processes which does not result in particle oxidation; thus increasing quality of deposited coating.